We all know lead acid batteries – they’re in our cars and start our generators. Solid workhorses, they are cheap and reliable, yet they do require a lot of maintenance.
One of the newest commercial batteries is lithium ion. Lithium ion batteries account for the largest share (59%) of operational installed capacity according to the International Renewable Energy Agency (IRENA) 2017 report Electricity Storage and Renewables: Costs and Markets to 2030. They are lightweight, have a high energy density and can be fully depleted without issue. This is important with variable solar energy, which won’t always be able to charge the battery.

Battery storage plays a significant role in the future of renewable energy generation
Energy storage systems
As an important part of a future with renewable energy, batteries are here to stay. As proof, the National Electrical Code introduced a new section in 2017 on Energy Storage Systems (ESS), Article 706. Important sections include:
- 706.10(A) requires ventilation to diffuse gases
- 706.10(C) states free air space is needed for a battery shelf for not less than 90 percent of its length
- 706.31(A) mandates antioxidant material be used to prevent corrosion
- 706.31(B) mandates the ampacity of intercell and intertier connectors be large enough to not exceed the safe operating temperature of the conductor insulation or supports. Thermal imagers are used to ensure these requirements are met.
The NEC 2020 will apply to batteries under 60 V dc (to cover lead acid batteries) and include a new section 705.13 Power Control Systems to allow for greater current on load-side connections necessary for alternating current (ac)-coupled ESS.
How to maintain batteries
Batteries are sensitive. They work best between 15 and 35 °C and require a charge controller to receive a specific amount of current. At low temperatures the electrochemistry is slowed, and at high temperatures internal corrosion is increased.
You probably have experienced a car not starting in cold temperatures – that’s because the battery cannot deliver as much current. In cold climates, use a battery heater or thermal insulation, and in hot climates store them in shaded, well-ventilated spaces.
Another issue is terminal corrosion. This happens when hydrogen gas is released from the acid in the battery reacting with other substances, or electrolyte leaking from overfilling with water or overcharging. To remove corrosion, use antioxidant material per the manufacturer’s recommendation.
For lead acid batteries, it is critical to ensure a high state of charge (SOC). Lead acid batteries have a low depth of discharge, meaning a small amount of its total capacity should be used. Too low a SOC and you have sulfation, buildup of small sulfate crystals on the terminals, which reduces performance. To handle sulfation on the terminals, techs need to keep the SOC high and if it gets too low use a desulfating battery charger to dissolve the sulfates with high frequency electronic pulses. Also, an alarm can be used with a visual and audible indication to alert a low battery state of charge (50% for lead acid).
How to diagnose battery health
Techs need to know the internal health of the battery to maintain them. Using the Fluke 500 Series Battery Analyzer, connect the leads to the negative and positive terminals and turn the switch to millohms (mΩ). The display will simultaneously read battery voltage and internal resistance. Low voltage indicates a low state of charge and high internal resistance means internal deterioration. It is important to test the battery in open circuit state (after 24 hours for lead acid batteries). The Analyzer corrects for temperature to ensure accuracy, saves 10 thresholds, and sends the readings to the Fluke Battery Management Software to view trends.
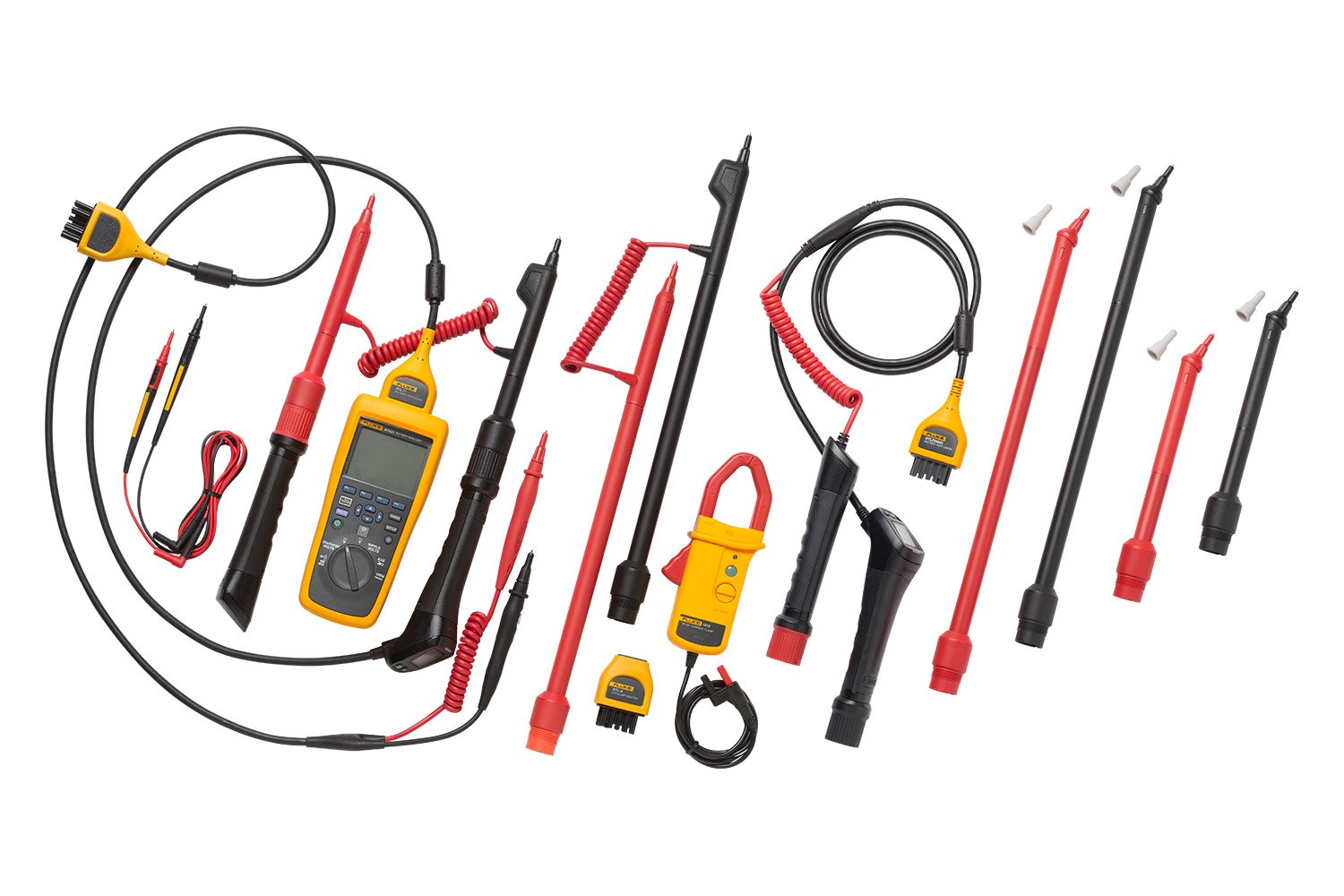
The Fluke 500 Series Battery Analyzer is the ideal test tool for maintenance, troubleshooting and performance testing of individual stationary batteries and battery banks used in critical battery back-up applications.
Capacity loss means the battery stores less charge. Techs can find the capacity loss using the Analyzer in discharge mode where battery voltage is read multiple times until it goes below the cut-off voltage, below which could cause damage.
A hydrometer, which measures the relative density of liquids, can also be used to measure electrolyte specific gravity, an indicator of a battery’s state of charge.
Evolution of energy storage technology
Though more expensive than lead acid, lithium ion batteries, such as Tesla’s Powerwall, represent a significant improvement from a maintenance perspective. While you need to regularly check their SOC and keep them as close to 25 degrees C as possible, they have higher energy density, making them lighter. They also have higher depth of discharge, meaning much of their charge can be depleted before recharging, which is great for variable solar and wind power.
Thermal runaway, in which overcharging, a short circuit, or high temperature creates a feedback loop that rapidly accelerates temperatures until explosion, is an issue. Using a cathode with a higher temperature tolerance, such as iron phosphate (FePO4), mitigates thermal runaway.
New battery technologies, such as saltwater and liquid metal batteries, which promise both low maintenance and cost are coming on the market.
Importance of battery maintenance
The answer to whether batteries are worth it for your facility comes down to priorities and costs. Lead acid batteries have low upfront costs but high ongoing maintenance costs, adding weekly cleaning, testing, and top-up tasks. On the other hand, lithium ion batteries have high upfront costs but low ongoing maintenance costs.
Regardless, as lithium ion and other non-lead acid battery costs decline and adoption of solar and wind grow, batteries will be an increasingly essential part of a facility.
About the expert
Michael Ginsberg is a solar expert, trainer for the U.S. Department of State, author and Doctor of Engineering Science candidate at Columbia University. He is also chief executive officer of Mastering Green, where he has trained nearly a thousand technicians worldwide in solar PV installation, maintenance, and operation.