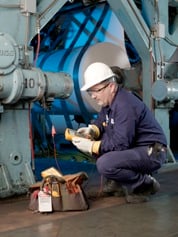
In Part I of this short application note series, we discussed inspection points on motors to make during an energy audit or other efficiency program. Part I covers basic motor efficiency strategy and describes tests and cost savings for voltage and current unbalance and for power factor.
Part II covers inspection points that are best incorporated into regular, long-term preventive maintenance:
- Off-design voltage
- Bad grounding and connections
- Insulation resistance
This application note also explains how to conduct inrush current testing, either during new high-efficiency motor installation or when troubleshooting new installs.
Off-design voltage
A three-phase induction motor is designed to operate within ±10 percent of the rated voltage on its nameplate. Operating motors significantly above or below their rated voltages ("off-design voltage"¹) affects their efficiency and other operating parameters.
Under-voltage can cause damage to motors if it is excessive. A fixed mechanical load on a motor requires a certain amount of power to do the work. Since the amount of power the motor must draw is roughly the product of the voltage and the current, if the voltage decreases, the current (amps) must increase to do the same amount of work. If the current drawn exceeds the full-load value specified on the motor's nameplate, overheating and damage likely will occur over time.
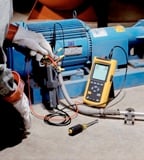
Under-voltage might cause production stoppages because the effects of low voltage are compounded during starting and acceleration. That is, under-voltage can affect the ability of a motor to overcome the inertia of its load at startup and slow its acceleration to full running speed. Typically the running speed stabilizes just slightly below normal but within ±10 percent of its nameplate value. However, so-called breakdown torque is reduced, and the motor is less capable of driving through a brief torque overload without stalling.
Over-voltage, in full-load situations and when it's within the +10 percent range of the nameplate value, actually enhances the efficiency of a motor. However, at reduced loading, efficiency improves with lower voltages as long as they are within -10 percent of the nameplate value. Since under-voltage increases current, it might seem that over-voltage will decrease current. That is not the case. In fact, at significant over-voltage, a motor draws more current in attempting to compensate for the effect of the over-voltage on the windings. The result is overheating.
Measuring off-design voltage from supply to motor terminals can be accomplished using some combination of a digital multimeter (DMM), clamp meter and a power quality analyzer. If the voltage anomalies are sporadic - spikes and/or sags - the best way to pinpoint their source may be to connect an electronic meter with waveform capture capabilities. This allows you to correlate off-design voltage events with other events in the facility. However, the first indication that there is excessive under- or over-voltage might show up in an inspection of motors using an infrared thermometer or imager.
Correcting off-design voltage entails trying the following remedies:
- When voltage is constantly and consistently over- or under-voltage by the same amount, change the main service transformer's tap setting, and adjust branch or secondary transformer settings.
- To correct daily voltage variations at the service entrance, install a transformer with an automatic tap changer.
- For voltage variations throughout a facility but not at the service entrance, replace or augment existing conductors and replace transformers as necessary.
- Use capacitors to correct power factor at points of use.
Potential savings and ROI
To calculate the potential savings and ROI resulting from actions to correct off-design voltages, you need to know the following (sample values are in parentheses):
- number of hours per year a stalled motor stopped the process (30 hr),
- annual income from the process ($2,500,000),
- number of days per year the process runs (365 days/yr),
- number of hours per day the process runs (24 hr/day),
- cost of the corrective device or component ($7,000),
- labor rates for corrective action or installation ($50/hr),
- number or electricians, etc. required (2), and
- estimated hours to do the job (10 hr).
Using the sample numbers, the annual lost income (L$) from downtime would be:
L$ = 30 hr x [$2,500,000 ¸ (365 days/yr x 24 hr/day)] = $8,562,
and the cost of the corrective action (C$) would be:
C$ = $7,000 + [2 x ($50/hr x 10 hr)] = $8,000.
So, the payback period for the investment is expected to be less than a year.
Bad connections and grounding problems
Regularly inspecting your electrical distribution systems for bad connections, poor grounding and shorts to ground will help improve equipment performance and avoid system outages and premature equipment failure.
Detecting bad connections, poor grounding and shorts to ground should be carried out by an experienced electrician or power specialist. These conditions can often be found by a visual inspection for looseness, corrosion or conductive paths to ground. Another telltale method for finding problem connections is to look for overheating at connections using an infrared thermometer or a thermal imager. Look, too, for voltage drops across connections. Compare all three phases. A voltage variation of two or three percent among connections suggests a need for corrective action.
Corrections can often be accomplished by regular cleaning and tightening of connections. You can also use an insulation multimeter to check starter and control contacts and to measure the insulation resistance of the line and load circuits to ground. These latter tests are important because you may find that you can get a motor back into operation with a fix as simple as replacing a cable.
Potential savings and return on investment (ROI)
Production savings from correcting bad connections, poor grounding and shorts to ground can be calculated if you know the cost of downtime for the process affected. Left uncorrected, a loose or corroded connection, poor grounding or a short to ground could blow a fuse and take down an entire production process.
Insulation resistance
Failure to find degraded insulation in electro-mechanical equipment can lead to motor failure and lost production. The best method is to integrate regular insulation checks into your preventive maintenance schedule.
Measuring insulation resistance directly requires the services of an experienced electrician or power specialist and the delivery of a high voltage, low direct current signal to de-energized systems. Both megohmmeters and insulation multimeters can supply such test current and pinpoint breakdown strength of electrical insulation. Before doing any insulation resistance testing, you must isolate from the circuit under test any electronic controls and other devices. Be sure to lock out and tag the disconnect to the motor starter.
When a motor is having problems and you are certain the voltage supply is nominal, use a megohmmeter or an insulation multimeter to check for insulation degradation.
The DOE recommends testing winding resistance phase to phase and phase to ground in motors twice a year.² Since insulation resistance varies with temperature and humidity, you may over time need to make several winding resistance measurements to get meaningful results. It's best to track insulation resistance measurements over-time, regardless, so that you're not caught by surprise. Determining what is a "good" or "bad" reading is depends on circumstance, however Fluke does offer an insulation resistance chart.³
General guidelines
- At less than 25% difference, the equipment is probably still operating acceptably (leakage clamp okay)
- At 25-50%, most professionals recommend additional and more frequent testing (using an insulation resistance tester)
- At >50%, most professionals would view this as indicative of potential problems, though equipment may continue to run for some time before failure.
Ground testing line and load circuits at the starter will identify the resistance to ground of the starter, line circuits to the disconnect, and load lines to the motor and starter windings. General thresholds: ac devices can safely operate at not less than two megohms to ground and dc devices can safely operate at not less than one megohm to ground. When measuring the resistance of a three phase motor between the load legs of the starter, you should see high resistance and roughly equivalent measurements between phases.
Measuring insulation resistance can also be done while equipment is operational, by using a leakage clamp meter to measure leakage current from the device. Leakage clamps, such as the Fluke 360, have specially designed jaws that eliminate the influence of adjacent current conductors and minimize the effects of external magnetic fields, even at low currents. Leakage currents can be an indicator of the effectiveness of insulation on conductors. High levels of leakage current may be present in circuits where either the insulation resistance is low, or electronic equipment with filters have been used. Leakage currents can cause disruptions of the normal operation of equipment and installations. The big advantage of leakage current testing versus insulation testing is the ability to measure during normal operations.
Correcting insulation resistance can be achieved by de-rating the motor in accordance with NEMA standards, if it will not too greatly impact production. Under any circumstances, generate a work order to replace the motor as soon as possible with a high-efficiency motor, if operating conditions warrant the upgrade.
Potential savings and ROI
To determine whether insulation degradation merits a motor replacement, try using these tools:
- Use MotorMaster+ software.
- Calculate potential savings from motor rated horsepower (hp), load factor, annual operating hours, average energy costs, efficiency of the motor being replaced and the efficiency rating of the new motor. (See the sample calculation in the Current Unbalance section in Part I of this application note.4)
Recall that premium efficiency motors are about one percent more efficient than standard efficiency motors, and the energy savings will typically result in a payback period of less than 18 months.
Inrush
If you've replaced older motors with high-efficiency models, you may encounter inrush problems. Granted, the older models being replaced were probably out of spec, worn, and didn't have any compensating electronics. However, high-e models can sometimes generate substantially more initial start-up current - or inrush current -than their operating or steady-state current.
While all motors draw inrush current, it is greater in high-efficiency motors. In a three-phase motor, for example, inrush current generally lasts about 100 milliseconds with a current spike between 500 and 1200 percent. While short lived, this surge can create problems, the most annoying of which is tripping the over current protection device (OPCD).
Inrush current can be five-to-twelve times the normal running current, depending on the type of motor. For example, if the running current of a motor is 8 A and the starting current multiplier is five times the running current, your inrush measurement should read about 40 A, even though the circuit breaker is rated for 20 A.
The reason the breaker or overload unit does not trip is because both of these devices have a time versus current curve that indicates how much current for how long a period they will pass without opening the circuit. Tripping can also be based on temperature - temperature can build up slowly during continuous operation, or more quickly during startup, but when the maximum temperature threshold is reached, the circuit trips.
Measurements
Start by measuring inrush current at startup. Use a tool specifically designed for inrush, such as the Fluke 337 Clamp Meter, that will automatically synchronize your measurement starting point with the motor's start point. Your tool's inrush function will take a large number of sample measurements during the startup period, filter them, and calculate the actual starting current.
Note: Don't try to use Min/Max to capture inrush - Max current can measure a momentary spike in power, but an Inrush feature measures the same energy delivered to the motor that the APCD measures and trips on. Max current measurements used to work on old models, but more advanced electronics mean more noise on signals, too much for an accurate inrush measurement.
Correcting Inrush
If the running current or temperature is too close to the continuous rating of the circuit breaker, then the motor will usually cause the breaker to trip on starting almost all of the time. Since inrush is always factored in for breaker sizing before installation, when upgrading to new more efficient motors, it may be necessary to upgrade the motor circuit protection to a newer type motor rated circuit breaker with adjustable instantaneous trip settings.
Notes
- ¹ The information in this section can also be found in the source document, Motor Tip Sheet #9 (June 2008), "Improve Motor Operation at Off-Design Voltages," an Energy Tips - Motor document written for DOE's Industrial Technologies Program.
- ² DOE's fact sheet: "Optimizing Your Motor-Driven System."
- ³ Insulation Test Guide (.pdf)
- 4 Electric Motors (.pdf)