DC services specialist deploys battery analyzer to maintain critical UPS systems
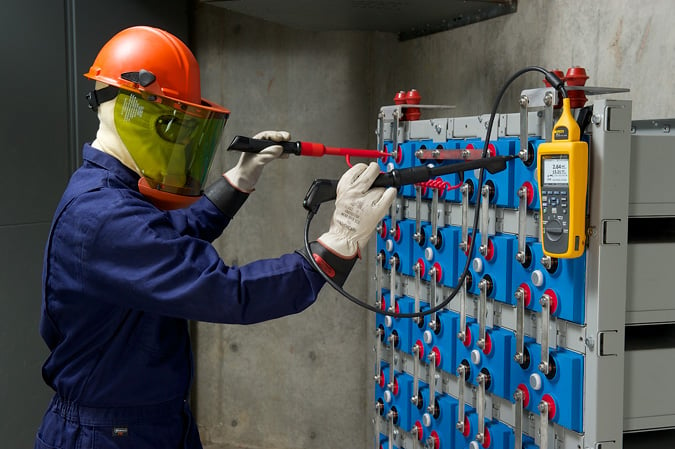
Emerson Network Power is the world's leading provider of critical infrastructure technologies and life cycle services for information and communications technology systems. Its Electrical Reliability Services (ERS) business offers complete solutions to maintain electrical system reliability and safety at critical facilities such as substations, power and industrial plants, and data centers. Many services offered by ERS involve maintaining uninterruptible power supply (UPS) systems.
Critical battery backup for critical systems
We recently spoke with Kris Klosowski, Industrial DC Services Specialist with ERS about how he uses the Fluke BT521 Battery Analyzer to maintain and troubleshoot UPS systems. Klosowski, a certified International Electrical Testing Association (NETA IV) technician, covers a wide territory west of the Mississippi River and north of Kansas City. In one facility, he might test a single UPS system, and in the next, he might test 50 systems.
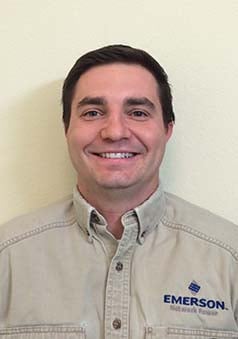
"Anything on a DC system is typically considered critical. It has battery backup for a reason, especially in power plants and substations," says Klosowski. "If a facility loses power, it needs a way to continue operating equipment."
A comprehensive battery maintenance program is necessary to ensure that in the event the backup batteries are needed, they are ready to do the job. Regular inspections, thorough testing including capacity testing, and continuous monitoring ensure maximum reliability, and help prevent deterioration from corrosion, internal shorts, dry-out, and seal failure.
The Institute of Electrical and Electronics Engineers (IEEE) has developed standard practices for battery maintenance, which includes testing capacity, internal and inter-cell resistance, and voltage. Power plants are subject to Federal Energy Regulatory Commission (FERC) and North American Electric Reliability Corporation (NERC) regulations, which require that they follow IEEE battery testing guidelines.
Support for IEEE battery testing guidelines
"We use the Fluke BT521 Battery Analyzer as a primary part of our battery testing, following IEEE guidelines," says Klosowski. "This helps us determine the condition of the battery. If we see low voltage or high internal resistance, we can tell that the battery either needs to be charged or replaced."
According to Klosowski, one of the differences between the Fluke BT521 and many other units on the market today, is that the 521 doesn't apply a load across the battery when measuring internal resistance.
"Some battery analyzers put a resistor across the battery, causing a small discharge which is used to calculate internal resistance," says Klosowski. "You might get a reasonable reading on the first few cells, but once you get to the end of the string, you're not really performing the same test, and your results may be skewed. With the 521, I get accurate readings without performing any discharge on the cells."
Unique timesaving features
Klosowski also notes some of the other unique features of the BT521 that save time. Because the BT521 provides built-in temperature measurements, he can measure negative post temperature at the same time as DC voltage and internal resistance, without having to carry an extra tool. The audio cues that tell technicians which cell they're on when testing a battery string help improve efficiency.
"When you're testing a long battery string, it's very easy to get lost," says Klosowski. "The Fluke battery analyzer tells you which cell you're on with every reading you take, making it easier to keep track and speeding up the testing process."
He also appreciates that the leads for the BT521 are more compact. "I find the 521 very convenient to use for a lot of reasons. The leads fit into tight spots that others can't. It responds quickly. And it's lighter to carry so it doesn't weigh down my tool bag," says Klosowski.