Most problems with single-phase motors involve the centrifugal switch, thermal switch, or capacitor(s). If the problem is in the centrifugal switch, thermal switch, or capacitor, the motor is usually serviced and repaired. However, if the motor is more than 10 years old and less than 1 HP, the motor is usually replaced. If the motor is less than 1/8 HP, it is almost always replaced.
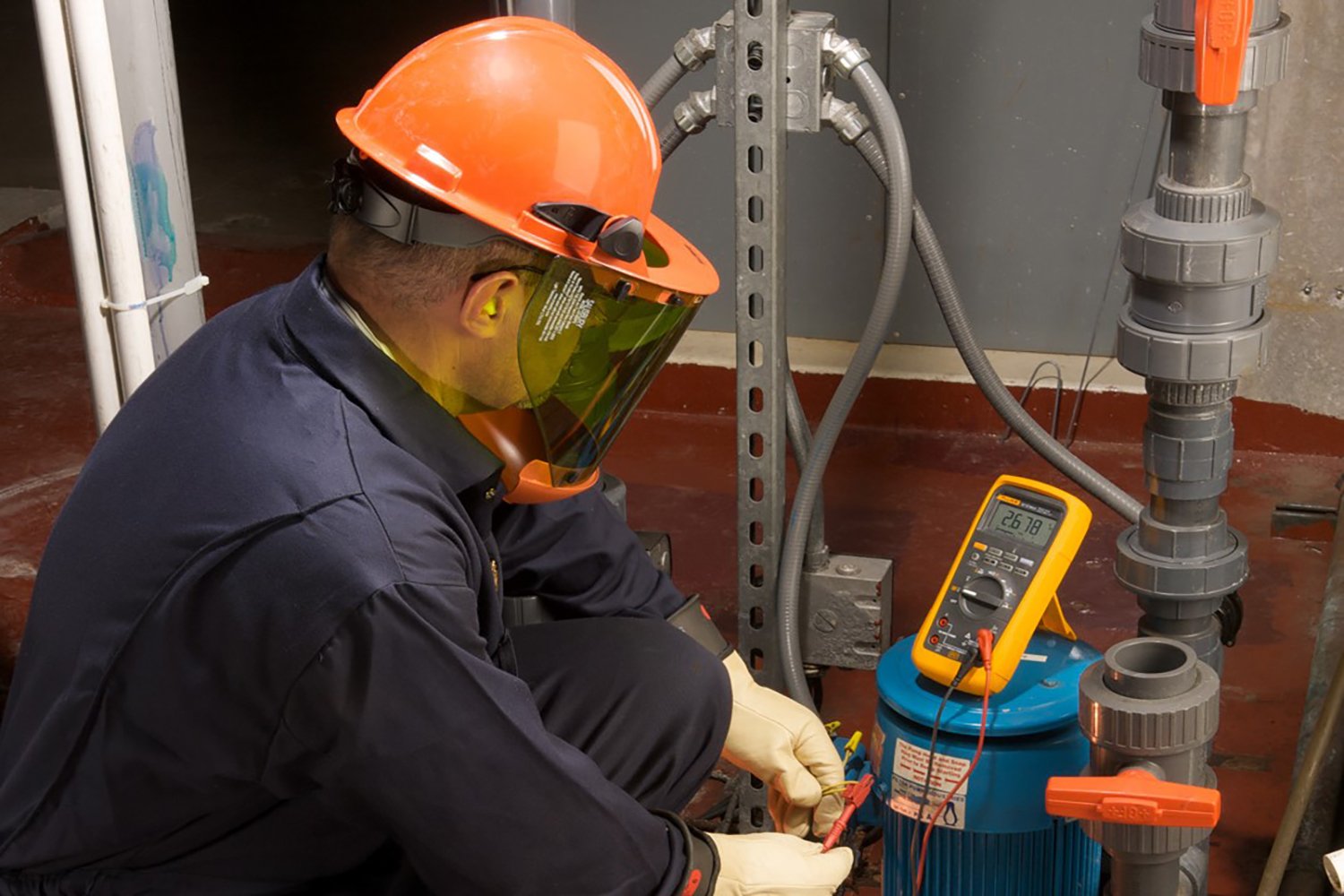
Troubleshooting split-phase (single phase) motors
The split-phase motor has a starting and running winding. The starting winding is automatically removed by a centrifugal switch as the motor accelerates. Some split-phase motors also include a thermal switch that automatically turns the motor OFF when it overheats. Thermal switches may have a manual reset or automatic reset. Caution should be taken with any motor that has an automatic reset, as the motor can automatically restart at any time.
To troubleshoot a split-phase motor, apply the following procedure:
- Turn power to motor OFF. Visually inspect the motor. Replace the motor if it is burned, the shaft is jammed, or if there is any sign of damage.
- Check to determine if the motor is controlled by a thermal switch. If the thermal switch is manual, reset the thermal switch and turn motor ON.
- If the motor does not start, use a voltmeter, such as a Fluke 87V Industrial Multimeter, to check for voltage at the motor terminals. The voltage should be within 10% of the motor's listed voltage. If the voltage is not correct, troubleshoot the circuit leading to the motor. If the voltage is correct, turn power to motor OFF so the motor can be tested.
- Turn the handle of the safety switch or combination starter OFF. Lock out and tag the starting mechanism per company policy.
- With power OFF, connect the Fluke 87V to the same motor terminals the incoming power leads were disconnected from. The ohmmeter will read the resistance of the starting and running windings. Since the windings are in parallel, their combined resistance is less than the resistance of either winding alone. If the meter reads zero, a short is present. If the meter reads infinity, an open circuit is present. In either case, the motor should be replaced. Note: The motor size is too small for a repair to be cost efficient.
- Visually inspect the centrifugal switch for signs of burning or broken springs. If any obvious signs of problems are present, service or replace the switch. If not, check the switch using an ohmmeter.
Manually operate the centrifugal switch. (The end bell on the switch side may have to be removed.) If the motor is good, the resistance on the ohmmeter will decrease. If the resistance does not change, a problem exists. Continue checking to determine the problem.
Troubleshooting capacitor motors
A capacitor motor is a split-phase motor with the addition of one or two capacitors. Capacitors give the motor more starting and/or running torque. Troubleshooting capacitor motors is like troubleshooting split-phase motors. The only additional device to be considered is the capacitor.
Capacitors have a limited life and are often the problem in capacitor motors. Capacitors may have a short circuit, an open circuit, or may deteriorate to the point that they must be replaced. Deterioration can also change the value of a capacitor, which can cause additional problems. When a capacitor short-circuits, the winding in the motor may burn out. When a capacitor deteriorates or opens, the motor has poor starting torque. Poor starting torque may prevent the motor from starting, which will usually trip the overloads.
All capacitors are made with two conducting surfaces separated by dielectric material. Dielectric material is a medium in which an electric field is maintained with little or no outside energy supply. It is the type of material used to insulate conducting surfaces of a capacitor. Capacitors are either oil or electrolytic. Oil capacitors are filled with oil and sealed in a metal container. The oil serves as the dielectric material.
More motors use electrolytic capacitors than oil capacitors. Electrolytic capacitors are formed by winding two sheets of aluminum foil separated by pieces of thin paper impregnated with an electrolyte. An electrolyte is a conducting medium in which the current flow occurs by ion migration. The electrolyte is used as the dielectric material. The aluminum foil and electrolyte are encased in a cardboard or aluminum cover. A vent hole is provided to prevent a possible explosion in the event the capacitor is shorted or overheated.
AC capacitors are used with capacitor motors. Capacitors that are designed to be connected to AC have no polarity.
To troubleshoot a capacitor motor, apply the following procedure:
- Turn the handle of the safety switch or combination starter OFF. Lock out and tag the starting mechanism per company policy.
- Using a Fluke 87V, measure the voltage at the motor terminals to make sure the power is OFF.
- Capacitors are located on the outside frame of the motor. Remove the cover of the capacitor. Caution: A good capacitor will hold a charge, even when power is removed.
- Visually check the capacitor for leakage, cracks, or bulges. Replace the capacitor if present.
- Remove the capacitor from the circuit and discharge it. To safely discharge a capacitor, place a 20,000-ohm, 2 W resistor across the terminals for five seconds.
- After the capacitor is discharged, connect the Fluke 87V leads to the capacitor terminals. The Fluke 87V will indicate the general condition of the capacitor. A capacitor is either good, shorted, or open.
Set your Fluke 87V to measure capacitance. The capacitance value read should be within ±20% of the value on the capacitor label.