Voltage detectors are a quick, inexpensive way to check for the presence of live voltage on ac circuits, switches and outlets before working on them. Also known as voltage wands, sticks, "power sniffers" or pens, they clip into a shirt pocket and beep or glow when they detect voltage on exposed conducting parts or through insulation.
These types of voltage detectors are designed for non-contact, live-not live voltage detection on electrical circuits found in residential, commercial and industrial buildings. Incidental contact with live electrical conductors is not an issue as long as the detector is rated appropriately for the voltage level and the electrical safety category in which it will be used. In addition, the user must exercise safe work practices and wear any appropriate PPE required.
Voltage detector safety
By telling you whether or not a circuit is live before you work on it, voltage detectors provide a critical safety function. However - getting safe, reliable readings requires purchasing the right kind of voltage detector for your work environment and then following these guidelines.
Always verify that the voltage detector is working properly before you rely on it. Use the detector to test a known live circuit both before and after you test an unknown circuit, and make sure it gives you the proper response. The same practice applies to multimeters. If there is any doubt in your mind about whether the circuit is truly live or dead, use an additional method to verify the test results. You only have to be right once to make it all worthwhile.
Note: Some voltage detectors, such as the updated Fluke 1AC II, have a self-test function built-in that will verify whether the detector is operational.
- Ensure that the voltage detector you are using is appropriately rated for the measurement environment you're working in and is within the voltage range you're testing. Industrial environments are generally CAT III or CAT IV. Not all voltage detectors are safety rated, however, and they're not equally sensitive. Some detectors will read small levels of voltage that others won't detect at all. Don't assume that the detector you're using now will perform the same as others you've used in the past.
Capacitive voltage detectors have certain limitations. Correct operation depends upon the capacitance between the detector's barrel and ground (normally through your hand and body). If this path is broken for any reason, the detector probably won't work. For example, if you're standing on a wooden ladder, the capacitance between your body and ground will be much less than if you were standing on a concrete floor. To help avoid incorrect detector readings, find an installation ground that you can touch when using the voltage detector. Remember, in a series circuit, the smaller the capacitance, the greater the voltage drop: there might be too much voltage drop from you to the floor and too little across the detector. The detectors will also have a certain minimum voltage to turn on. In our wooden ladder scenario, the detector might not turn on despite the circuit being hot. By similar reasoning, the detector cannot detect live conductors inside a grounded metal conduit.
For best results always hold the detector by the body and remember to keep your fingers away from the tip of the detector.
Favorite applications from the field
Most technicians use their voltage detectors daily, to verify power is off before working in an electrical area and to quickly map circuits. However, like most such practical tools, real-life offers many other applications for a good voltage detector.
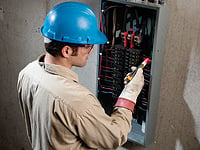
By David Welch
I work in an extremely corrosive atmosphere. On this particular day our crew was to disconnect a 480 volt motor. No big deal: we shut off the breaker and tested the circuit with a standard volt tester. It didn't show any voltage when the leads touched the screws on the breaker phase to phase and phase to ground. I happened to have my Fluke 1AC tester in my pocket and decided to test the load side of the breaker. The Fluke tester showed voltage on C phase where the breaker had failed to open. The breaker failure was a result of that phase in the motor grounding. The test leads on my other tester did not show the voltage, due to the amount of corrosion on the screws. The Fluke tester with its inductive capabilities might just have saved a life. From this day forward I always double check with my Fluke 1AC tester. Safety is the number priority and we now issue everyone a 1AC tester as standard issued test equipment.
By Logan Cleek
Well my truck started acting up, running rough etc. Not being an auto mechanic I didn't have any diagnostic tools for that. So I grabbed my Fluke 1AC pen, held it by all four plug wires, and found one that was flashing different than the rest. So, I pulled that plug and found that it was fouled and its plug wire was bad.
By Michael Hays
I'd been helping the plant electrician do the industrial shop lighting repairs/PM's. Up until recently, it was a two, sometimes three man job - two in our Manlift, and a third on the ground, to find and switch off power to the various light banks. Since equipping ourselves with Fluke volt pens, we've reduced the 'men' to two, and on week ends, just one, as we now can quickly and safely check the presence of 440 V ac on our lighting, as well as other basic voltage checks, throughout the plant.
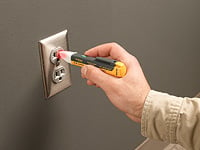
By Scott Cleveland
I was getting ready to perform a repair on a major machine at the plant and used a Fluke 1AC to spot check. I found a breaker someone had rewired without updating the drawings and bypassing the lock-out point. I started checking with my multimeter and it did have live 480 volts on a breaker that should have been dead. We now give 1ACs to all of our trouble shooters and PM crew. It's so easy to check with, and we have also used it to trace circuits. In once case, we isolated the circuit, powered it, and used the 1AC to follow the circuit through several cabinets until we found the trouble. It saved a lot of downtime.
By Nathan Kane
I was working on 277 volt overhead lighting with another electrician. We needed to make sure the power was off. So he used his voltage detector to check if there was power. He had just put new batteries in his detector, and it showed no sign of life in the wires. So, he was going to start working. But I have a fluke 1AC voltage detector and I climbed up the ladder and tested the wires with my tester. The Fluke showed that the power was still on. That little tool saved us from possible shock. I also use the tester to make sure receptacles aren't wired backwards - I've found that a lot just by using the 1AC.
By Eric Lewis
My company services professional lighting, audio and video equipment. That means dark night clubs and back stages with minimal work light. The Fluke LVD1 and the 1AC get used every day when working on site. The LVD1 is perfect for clipping to a piece of equipment, allowing us to actually see what we are doing, and its voltage detector capability has paid for itself by finding breaks in ac power cables and letting us know if the power is getting to a component or not. Many of the things I fix have internal fuses, and the 1AC detector can quickly tell me if I need to disassemble a piece or just replace the ac cord. They are also indispensable in live 'rock and roll' shows for finding if a stage drop (extension cord, or 'stinger') is hot. If I'm on a show, the 1AC is in my tool pouch!
By James Turba
Normally the individual bulbs on a new Christmas light strings have internal shorting fuses that maintain circuit continuity when the filament opens. But every so often, the wire leads break or lose contact. When that happens, all the lights in that series go out and you have to check each bulb to find the problem. Instead, put your 1AC voltage detector near the bulb socket wires at each end of the string to identify the "Hot" wire. Then go to the mid point and check the socket wires for voltage. If voltage is present, go half way back and check again. Keep narrowing down until you have a target area and then check those bulbs until you find the bad one. This won't work if the string has a third "hot" wire, or if it has the older kind of bulbs.