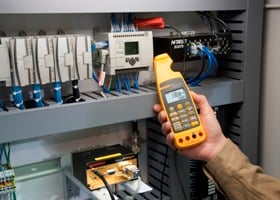
Early reports from the field suggest that the new Fluke 772 and 773 Milliamp Process Clamp Meters may be game changers, breaking new ground for technicians in the HVAC controls industry. With the feature sets these meters offer, troubleshooting of the most common problems in modern control systems becomes a snap.
Common applications for these meters include communications measurement, milliamp loop sensor measurement, damper and valve actuator troubleshooting, and troubleshooting the operation of variable frequency drives (VFDs). Let's look at some typical scenarios for each of these examples.
Communications measurement
A controls technician receives a too-hot complaint from a room on the third floor of a building on campus. A quick check of the BAS front-end computer reveals that the variable air volume (VAV) box controller is offline, not communicating. The technician grabs his new Fluke 773 and heads out to the building.
- After reaching the room, a quick check of the VAV box in the ceiling reveals that the VAV damper is in the closed position. The VAV controller normally has an LED that blinks when the controller is online. That LED is off.
- The technician quickly attaches his Fluke meter to the RS-485 Communication bus wiring terminals and measures the proper voltage, reading approximately +2.5 V dc between the three terminals, labeled +, - , and ref.
- A quick check of the wiring shows that the communications connector was not fully seated, causing a communications loss.
- After seating the connector properly, the VAV box controller comes back online, the communications LED resumes blinking, and the VAV damper begins to stroke open.
- A call is then placed to the operator in the control room and the controller is now online. The room immediately begins to cool down.
Milliamp loop sensor measurement
The foundation of each model in the 771/772/773 Milliamp Clamp series is the groundbreaking ability to troubleshoot milliamp sensors inside crowded control panels - without breaking the circuit. In this scenario, our technician notices that the static pressure inside the supply duct of a VAV system seems to be too high.
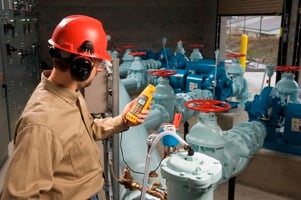
- A check of the BAS front-end computer indicates that the sensor is reading a perfect 1" WC of static pressure.A check of the actual static pressure using an airflow meter such as the Fluke 922 indicates that the static pressure is actually 1.5" WC. For these systems, 1' WC is considered normal.
- The technician takes his 773 Milliamp Clamp out to the control panel and finds the wires that terminate the static pressure sensor to the controller. As in many of the control panels in this building, the wiring looks like cooked spaghetti. The small jaws of the 772/773 enable the technician to clamp the exact wires perfectly. He reads the milliamp signal and compares it to the listed range for the sensor. The sensor is 0 - 20 mA and has a range of 0 - 2" WC. It is currently reading 15 mA. At 1" WC it should be reading 10 mA.
- The technician uses his laptop and opens up the program in the controller. He finds that the programmer did not scale the sensor properly in the software, which caused the error.
Damper and actuator troubleshooting
Another controls technician receives a too-cold complaint from an office in the building. The system is VAV with a hot water reheat valve.
- A quick look determines that the valve is closed. She connects her laptop to the controller and uses it to commission the controller. She attempts to override the valve open, but without success.
- She disconnects the wires to the actuator from the controller and then connects to the Fluke 773. She uses the meter to send a 0 - 10 V dc signal directly to the valve actuator to make it open and close. The valve actuator then works perfectly.
- Reviewing the controller programming, the tech determines that the reheat valve was forced closed by an improperly operating interlock, which is then removed. After this, the reheat valve works properly and the space warms up.
Troubleshooting VFDs.
During a spell of hot weather, all the occupants of a building complain that it is too hot.
- The chilled water pump system uses a VFD, but its operating pressure is too low.
- The controller sends a milliamp signal to the drive to command it to the correct frequency to obtain the correct system pressure. A tech disconnects the system controller, connects the Fluke 773 directly to the terminal block of the VFD, and generates a milliamp signal to the drive to increase the speed. Despite generating a 100% signal to the drive, it never comes up to speed.
- A check of the recorded fault statuses of the drive indicates that a circuit board has failed. The manufacturer is contacted and the faulty board replaced, at which time the drive operates correctly again and the chilled water system returns to the correct pressure.
In these common scenarios, the Fluke 772 and 773 meters are already proving themselves in the wide range of troubleshooting situations encountered in today's buildings. Every controls technician will want one in their tool bag.