Raaka-aineiden vaihtelevan hinnan vuoksi teollisuusyritysten on sopeuduttava vallitseviin tilanteisiin ja erilaisiin katteisiin. Yksi harvoista tavoista hallita kustannuksia koko teollisuudenalalla on keventää organisaatiota ja tehostaa toimintaa.
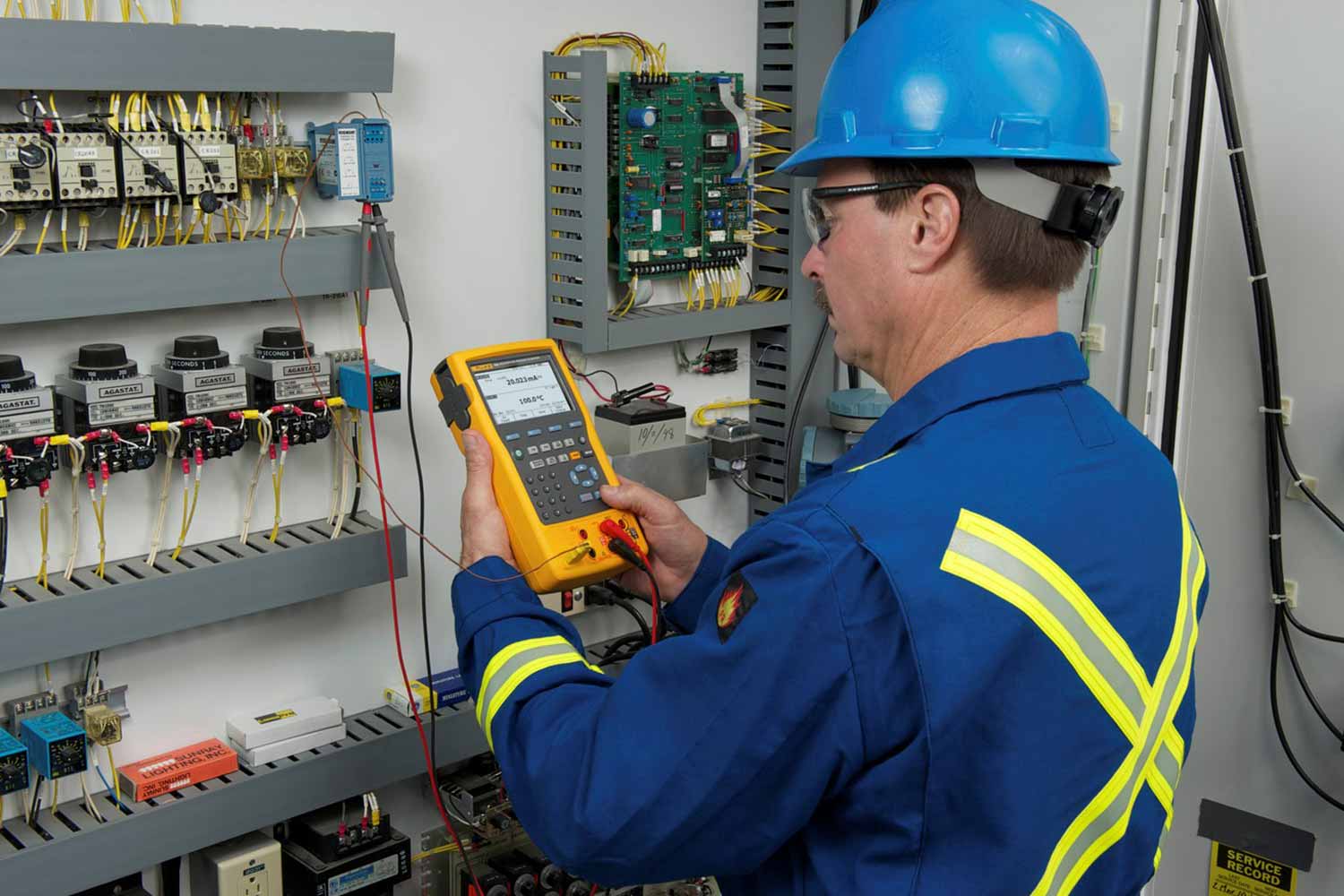
Yksi parhaista tavoista hallita näitä kustannuksia on tunnistaa, miten prosessissasi haaskataan resursseja. Instrumentaation osalta vaaditaan paljon hienosäätöä, jotta lämpötila ja paine saadaan kohdalleen laadukkaan tuotannon ja raaka-aineiden tehokkaan käytön kannalta.
Laitteiden kalibrointi optimoi tuotantoa ja parantaa laatua. Tämä pätee myös muihin prosessiteollisuuden aloihin, olipa kyse sitten kemianteollisuudesta, ydinvoimateollisuudesta, lääketeollisuudesta tai sellu- ja paperiteollisuudesta. Prosessitehtaissa on satoja, jopa tuhansia kehittyneitä laitteita, jotka suorittavat jatkuvasti lukemattomia kriittisiä toimintoja tarkasti ja luotettavasti. Nämä laitteet on puolestaan tarkastettava, testattava, kalibroitava ja korjattava säännöllisesti.
Vuosisatojen kokemus teollisuudessa on osoittanut, miten tärkeää näiden tarkastusten, testien, kalibrointien ja korjausten yksityiskohtien dokumentoiminen on. Yrityksillä ja valtioilla on usein oltava erittäin tarkka kirjanpito, jolla varmistetaan, että asiakkaat saavat laadukkaan tuotteen tai palvelun ja että kansalaisten terveyttä ja turvallisuutta suojellaan.
Perinteiset testaus-, kalibrointi- ja dokumentointikäytännöt vaativat kuitenkin myös paljon työtä, ja koska kokeneita työntekijöitä on vähän, pienennetyt tiimit saattavat toisinaan jättää säännöllisen kalibroinnin väliin. Teollisuudessa on vastikään huomattu, että pienet tiimit voivat suorittaa laitteiden kalibrointeja ja dokumentoida niitä siten, että kokonaiskustannukset laskevat, tuottavuus kasvaa ja toimintavarmuus paranee.
Kalibrointi tehdään tavallisesti joko laitteen sijaintipaikassa (in situ -kalibrointi) tai verstaalla.
Vinkki:
Kun kenttäinstrumentti on valmistettu, sekä primäärianturi että lähetin (tai käyttölaite, jos kyseessä on ohjausventtiili) kalibroidaan tehtaalla ja kalibrointitiedot toimitetaan laitteen mukana. Usein nämä kalibrointitiedot katoavat. Tiedot on syytä kirjata keskitettyyn kalibrointitietokantaan laitteen käyttöönoton yhteydessä osana vakiokäytäntöä eikä vain tehokkuuden vuoksi.
Laitoksen kalibrointitietojen keskittäminen varmistaa, että tiedot säilyvät silloinkin, kun tiimien jäsenet vaihtuvat.
Useimmissa kenttäinstrumenteissa on kaksi osaa: primäärianturi ja lähetin.
- Primääriantureita ovat muun muassa virtausputket; kuristuslaipat, paineanturit; märkäkemian anturit, kuten pH-, ORP- ja johtokykyanturit; kaikki tasomittarit ja lämpötila-anturit. Primäärianturit tuottavat tavallisesti jännite-, virta- tai resistanssisignaalin, jonka suuruus on suhteessa niiden mittaamaan muuttujaan, kuten tasoon, virtaukseen, lämpötilaan, paineeseen tai kemialliseen ominaisuuteen. Primäärianturit on kytketty kenttälähettimien tuloon.
- Kenttälähettimiä ovat paine-, lämpötila- ja virtauslaitteet. Ne käsittelevät primäärianturin tuottaman signaalin muuttamalla sen ensin lineaariseen muotoon ja sitten soveltamalla siihen erilaisia kertoimia käytetyn mittayksikön mukaan, minkä jälkeen ne lähettävät signaalin eteenpäin analogisessa (yleensä 4–20 mA DC) tai digitaalisessa muodossa (useimmiten jonkin kenttäväylän välityksellä).
Analogiset laitteet
Analogisia laitteita kutsutaan usein 4–20 mA virtasilmukaksi siksi, koska ne lähettävät signaalin, joka on analoginen esitys mitatusta fyysisestä suureesta (esimerkiksi lämpötila). Ne lähettävät virtaa, joka on verrannollinen (analoginen) mitatun fyysisen suureen arvoon. Signaalissa 4 mA virta vastaa pienintä skaalattua arvoa ja 20 mA virta suurinta skaalattua arvoa.
Vaikka monet järjestelmän osa-alueet ovat nyt digitaalisia, analogisia laitteita on yhä paljon käytössä kaikkialla prosessiteollisuudessa.

Digitaaliset laitteet
Digitaaliset laitteet muuntavat mitatun fyysisen suureen arvon digitaaliseksi signaaliksi. Prosessiteollisuudessa käytetään monia erilaisia digitaalisia koodausmenetelmiä, kuten Foundation Fieldbus, Profibus ja HART.
Yleinen uskomus on, että (digitaaliset) kenttälaitteet eivät vaadi kalibrointia. Tämä ei ole totta. Vaikka kenttäväyläsignaali (Foundation Fieldbus, Profibus tai HART) antaa diagnostista tietoa, se ei anna tietoja laitteen tarkkuudesta eikä varmista, että laite antaa prosessista tietoja tarkasti ja täsmällisesti.
Kolme parasta kalibrointityökalua, jotka pitävät prosessisi kunnossa
- Fluke 754 dokumentoiva prosessikalibraattori, jonka ominaisuuksiin kuuluvat HART-yhteensopivuus ja automaattiset kalibrointiproseduurit ja joka luonnollisesti on tiukkojen turvallisuusstandardien mukainen.
- Fluke 721 -tarkkuuspainekalibraattori, jossa on kaksi erillistä anturia, kaasun laskutus- ja myyntimittaussovelluksiin.
- Fluke 700G- painekalibrointimittarit ovat laadukkaita sekä kestäviä, ja ne takaavat nopeat ja tarkat mittaustulokset.
Ohjausventtiilit
Ohjausventtiileissä on toimilaitteet, jotka on myös kalibroitava kulumisen ja juuttumistaipumuksen vuoksi sekä vuotavan venttiilin tiivistämisen jälkeen. Jos näitä venttiileitä ei ole käytetty säännöllisesti, niille on usein tehtävä täydellinen tai osittainen iskutesti, jotta niiden luotettava toiminta voidaan varmistaa.
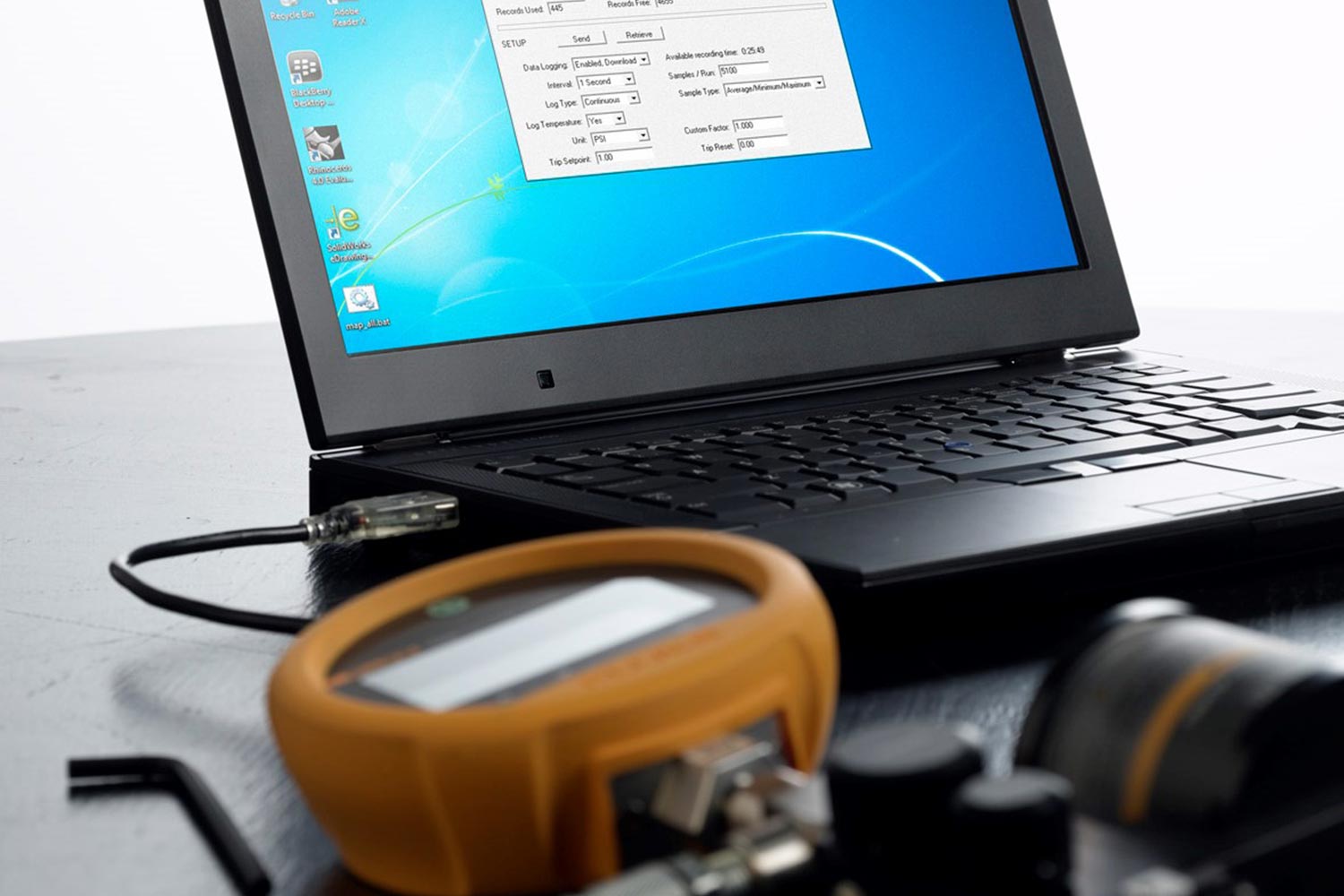
Luvat ja paperityö
Hallinnolliset tehtävät, kuten lupien hankkiminen ja tulosten dokumentointi sekä arkistointi, voivat jopa in situ -kalibroinnin yhteydessä lisätä kustannuksia ja viedä aikaa. Kuten Ian Verhappen, Industrial Automation Networks -yhtiön johtaja ja Fieldbus Foundation User Groupin entinen puheenjohtaja, on todennut: ”Monissa tapauksissa kaiken tarvittavan paperityön (luvat, eristäminen yms.) parissa kuluu enemmän aikaa kuin itse työssä.”
Kalibroinnin dokumentoinnin haasteet
Kalibroinnin dokumentointi on perinteisesti tarkoittanut sitä, että lokikirjaan merkitään päivämäärä ja aika, kalibroinnin valmistelun aikaiset lukemat, kalibroinnin jälkeiset lukemat ja muita tehtyjä havaintoja. Yllättävää kyllä, monilla tehtailla kalibroinnit kirjataan edelleen käsin. Käsin kirjoitetuissa asiakirjoissa on kuitenkin monia puutteita.
Ensinnäkin käsin kirjaaminen tuottaa virheitä, jotka säilyvät ja kertautuvat. Käsin kirjoitetut tiedot ovat usein lukukelvottomia tai puutteellisia. Tietokonepohjaista kunnossapidon hallintajärjestelmää (CMMS) käyttävissä laitoksissa tiedot on kirjaamisen jälkeen syötettävä järjestelmään käsin, mikä altistaa lisävirheille.
Henkilöstön vaihtuminen
Myös henkilöstön vaihtuminen vaikeuttaa kalibrointia.
1980-luvulla määrärahoja leikattiin ja työntekijöitä irtisanottiin. Suunnittelu-, ylläpito- ja käyttöhenkilöstöä vähennettiin merkittävästi ja jalansijaa sai uusi tuottamattomien toimintojen poistamiseen perustuva lean-ajattelu, joka on edelleen vallalla erityisesti teollisuusmaissa.
Pienemmillä tiimeillä on vähemmän aikaa mentorointiin ja työpaikkakoulutukseen, mikä johtaa siihen, että työntekijän omat tiedot järjestelmästä eivät siirry laitoksen yhteiseksi tiedoksi. Kun kokeneet työntekijät ja insinöörit jäävät eläkkeelle, myös yksityiskohtaiset tiedot laitteista ja järjestelmästä katoavat heidän mukanaan.
”Laitoksen koko tietämys kävelee portista ulos joka päivä neljältä iltapäivällä”, kertoo Yhdysvaltain keskilännessä sijaitsevan suuren jalostamon instrumentointi- ja ohjauslaiteosaston johtavainsinööri, ”ja toisinaan se ei enää palaa”.
Monissa laitoksissa in situ -kalibroinneissa tarvitaan edelleen kaksi henkilöä, joista toinen työskentelee lähettimen ja toinen ohjausjärjestelmän parissa. Fieldbus Foundation -säätiön arvion mukaan käyttöönottoon vaaditaan kaksi henkilöä ja vähintään kaksi tuntia aikaa.
Käytä dokumentoivia prosessikalibraattoreita
Uuden sukupolven kenttäkalibrointityökalut ovat entistä älykkäämpiä. Ne lisäävät työntekijöiden tuottavuutta, koska niihin on koottu useita työkaluja yhteen ja niissä on perustestien ja -mittausten lisäksi muitakin toimintoja, kuten analysoinnin ja dokumentoinnin aputoimintoja.
Dokumentoivat ja monitoimiset prosessikalibraattorit ovat kädessäpidettäviä elektronisia testityökaluja, joilla voi suorittaa useita eri kalibrointivaiheita ja joissa on useita eri toimintoja, kuten paineen ja lämpötilan sekä useiden erilaisten sähköisten ja elektronisten signaalien syöttö, simulointi ja mittaus.
Edut:
- Vähemmän työkaluja, joita on opeteltava käyttämään ja jotka on otettava mukaan kentälle
- Eri laitteiden kalibrointiprosessit ja tiedonsiirtostandardit ovat yhtenevät, kun taas perinteisesti jokaisen työkalun ja laitteen vaatima työtapa on ollut erilainen ja saatujen tietojen muoto on vaihdellut
- Automaattiset toimenpiteet korvaavat useita manuaalisia kalibrointivaiheita
- Toista henkilöä ei tarvita kirjaamaan as-found- ja as-left-tilan arvoja
- Lyhyempi laitekohtainen kalibrointiaika
- Yksittäisen työkalun virheen laskenta useiden eri työkalujen kumulatiivisen virheen sijaan
Käytä kalibrointireittejä
Suurimmat säästöt dokumentoivaa kalibraattoria käytettäessä ovat laitteen oman reitinhallintatyökalun ansiota. Kun käytetään yhtä lupa- ja lomakekokonaisuutta useissa kalibroinneissa, kustannukset vähenevät huomattavasti.
Ota käyttöön resurssien hallintajärjestelmä, kalibroinnin hallintajärjestelmä tai tietokoneistettu kunnossapidon hallintajärjestelmä (CMMS)
Toisin kuin paperisten asiakirjojen tiedot, kalibraattorin tiedot eivät koskaan ole epäselviä, vaikeasti ymmärrettäviä tai puutteellisia. Dokumentoivan kalibraattorin tiedot voidaan ladata suoraan erilaisiin CMMS-järjestelmiin ilman muuntamista tai kirjaamista.
Dokumentoivat prosessikalibraattorit tallentavat paikan päällä automaattisesti jokaisen kenttälaitteen as found- ja as-left-tilan ja ovat yhden henkilön käytettävissä, joten niiden käyttäminen yhdessä reittipohjaisten menetelmien kanssa voi säästää jopa 50 prosenttia perinteisten yksilaitteisten kalibrointimenetelmien kustannuksista ja kalibrointiin kuluvasta ajasta. Toisin sanoen sama pieni tiimi voi kalibroida samassa ajassa kaksi kertaa enemmän laitteita.
Jos pieni tiimi käyttää perinteisiä menetelmiä, virheiltä on vaikea välttyä. Kalibrointeja ei yksinkertaisesti tehdä niin kuin pitäisi. Häämöttävän uhan sivuuttamisen sijaan on syytä tutkia, miten olemassa olevia käytäntöjä voitaisiin parantaa.
Ota käyttöön reittipohjainen kalibrointi, paperiton dokumentaatio ja CMMS-tiedonhallinta. Kalibrointeja tehdään johdonmukaisemmin, tieto siirtyy yksilöltä tiimin ja laitoksen tasolle ja sekä tuottavuus että laatu paranevat.
Useiden laitteiden kalibroiminen samalla reitillä vähentää kalibrointikohtaisia kustannuksia verrattuna kunkin yksittäisen laitteen kalibroimiseen erikseen.
Tapaturmista aiheutuvat oikeudenkäyntien kustannukset ja tulonmenetykset voivat maksaa miljoonia. Hyvät kalibroinnin ylläpitokäytännöt auttavat huoltokustannusten säästämisen lisäksi vähentämään tapaturmien todennäköisyyttä. Jos tapaturma kuitenkin tapahtuu, laitos voi käyttää hyvää kalibrointikirjanpitoa osana puolustustaan, siinä missä huonoa kalibrointikirjanpitoa saatetaan käyttää oikeudenkäynnissä laitosta vastaan.