ROI on industrial energy efficiency cost savings
Wade Thompson es un especialista en calidad eléctrica de Fluke quien anteriormente trabajó para RPM y BMI. Se especializa en el diagnóstico y la solución de problemas de calidad eléctrica en centros de datos, sistemas embebidos grandes, empresas públicas e instalaciones industriales.
P. ¿Qué tiene que ver la medición con el ahorro energético?
Se trata del retorno de inversión y las finanzas. Las instalaciones necesitan consumir una cierta cantidad de energía para producir trabajo, productos, datos o cualquier otra cosa. Pero la mayoría de las instalaciones consumen demasiada energía. Son usuarios energéticos ineficientes. Hasta la década pasada, la gerencia de instalaciones como una industria no era importante, pues la energía era barata. Cuando la energía se volvió más cara, los gerentes se interesaron en reducir sus facturas de energía, pero había que poner el prospecto en términos del negocio: ¿en dónde se encuentra el punto de conversión del retorno de inversión en los casos en los que el desperdicio amerita abordarlo? Para responder a esa pregunta, necesita medir cuánta energía está consumiendo en los distintos tipos de trabajo (sistemas) en su edificio y compararla con los estándares. Esto le permite conocer la dimensión del desperdicio. Hacer mediciones adicionales puede ayudarle a identificar la raíz del desperdicio. La cantidad de desperdicio en combinación con la causa y el costo correspondiente son las tres variables de una ecuación de retorno de inversión.
P. ¿Cuándo es pertinente, para qué tipo de instalación, en dónde?
La reducción energética es pertinente en las instalaciones en las que se quiere reducir los gastos generales a fin de aumentar la productividad; instalaciones que quieren hacer más con menos, no solo gastar menos. Una inspección de eficiencia energética identifica las oportunidades para reducir los gastos generales y le da la información para entender qué actividades de ahorro de energía le convienen al gerente de la instalación, dados los objetivos principales de la instalación, y cuáles no ofrecen un retorno de inversión suficiente o definitivamente no son prioritarias. Las mayores oportunidades suelen presentarse en las instalaciones con grandes y antiguos sistemas de alto consumo energético que no han sido optimizados. Otros candidatos incluyen las instalaciones de producción que no han introducido mucha automatización ni controles, así como las instalaciones con grandes sistemas de vapor o aire comprimido.
P. ¿Cuánto puede ahorrarse?
Ojalá pudiera prometer que todas las instalaciones verán sus facturas de energía reducidas en 25 por ciento; ese es un promedio bastante común del potencial de ahorro que refiere el Departamento de Energía de EE. UU. (DOE). Los ahorros reales dependen de un par de cosas. Primero, ¿qué tipo de sistemas y actividades hay en su instalación? Las grandes cargas que no se han mapeado de acuerdo al programa de tarifas de la empresa pública para aprovechar los momentos más económicos del día tienen la promesa de lograr ahorros significativos. Las instalaciones que funcionan principalmente con cargas menores no tendrán la misma oportunidad. Segundo, ¿qué tan ineficientes son los sistemas del edificio? Una instalación más reciente, con un buen mantenimiento no ofrecerá tantas oportunidades de ahorro como una instalación más antigua en la que los sistemas y los equipos se han desviado de las configuraciones y las prácticas de mantenimiento recomendadas.
P. Cuando pienso en desperdicio energético, pienso en aire frío colándose por la ventana y en remplazar las antiguas bombillas con bombillas LFC. ¿Qué tipo de "desperdicio energético" ocurre en las instalaciones de fabricación o de uso mixto?
Ambas son buenas analogías, pues las dos ilustran el uso de energía en procesos ineficientes. El uso de energía para calentar o enfriar aire y empujarlo a través del sistema de ventilación, solo para que se cuele por la ventana, fuerza a que el sistema produzca de más y, por ende, consuma de más. ¿Qué otros sistemas en la instalación estarán trabajando más de lo necesario a causa de filtros obstruidos, motores sobredimensionados, etcétera? El uso de energía para encender bombillas incandescentes es ineficiente a causa del alto porcentaje de energía consumida que se desperdicia en forma de calor disipado. Traslade ese pensamiento a todos los equipos antiguos en una instalación que (posiblemente) consuman más energía para su funcionamiento que los modelos de alta eficiencia más recientes.
Por lo tanto, sí, una instalación de fabricación o de uso mixto puede experimentar desperdicios tanto en la iluminación como en el recubrimiento del edificio. Pero ¿son esos los primeros desperdicios que hay que abordar? No es posible contestar esa pregunta sin haber registrado el consumo eléctrico en todas las cargas mayores, mapearlo de acuerdo al programa de tarifas y al programa de operaciones y hacer los cálculos del retorno de inversión. Muy a menudo, las instalaciones logran los suficientes ahorros de operación y mantenimiento de equipos grandes que dentro de pocos años ahorran el dinero suficiente para acelerar el remplazo del equipo con un modelo más eficiente.
P. ¿Por dónde se empieza? Los presupuestos, el tiempo y los recursos son limitados.
Trabaje a partir de un punto de partida.
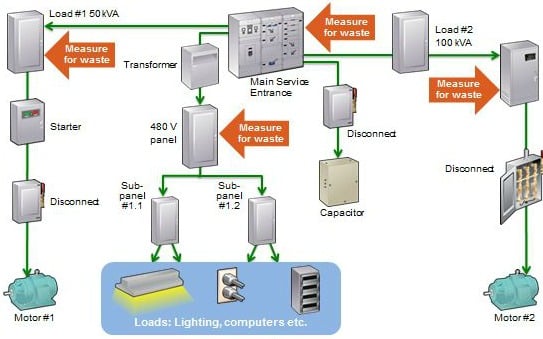
El comienzo es identificar el dónde y el cuándo se usa la energía, y por qué. Una vez que los propietarios, gerentes y técnicos de la instalación entiendan exactamente cuánta energía es necesaria para el funcionamiento del negocio y la comparen con la energía desperdiciada, entonces puede tomar decisiones y armar un plan. Para llegar a ello, comience por obtener copias de varias de las facturas más recientes de la empresa pública de electricidad y busque indicios de penalizaciones y cargos por demanda de energía en momentos pico. Descargue una copia del programa de tarifas del sitio web de la empresa pública, de modo que sepa el costo por unidad de energía en diferentes momentos del día, en comparación con su programa de operaciones. De ser necesario, llame al departamento de servicio de la empresa pública directamente; estarán encantados de que se ponga en contacto.
Entonces, instruya a su propio equipo de electricistas o a un contratista eléctrico para que registre la potencia en las entradas principales del servicio de la empresa pública, así como en los paneles de alimentación hasta los sistemas y las cargas más grandes. Registre los kW, kWh y el factor de potencia durante un periodo representativo. Esto brinda un panorama muy preciso del consumo de energía real en los circuitos trifásicos y las cargas. Los mayores ahorros suelen provenir del cambio de las operaciones de carga a las horas del día en que la energía es más barata.
P. Háblenos de estos sistemas que son los "desperdiciadores" más comunes.
Además del mapeo del sistema de alimentación eléctrica, siempre recomiendo que la gente evalúe sus sistemas de aire comprimido, de vapor y electromecánicos. Suelen tener múltiples usos de energía desperdiciada que puede repararse fácilmente.
Electromecánico
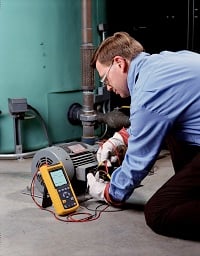
Existen cinco tipos comunes de desperdicio de energía en un sistema electromecánico: eléctrico, mecánico/de fricción, de programa, de control y de tamaño/eficiencia.
- La sobrecarga de corriente/tensión y el desequilibrio de fases son dos de las principales causas de desperdicio de energía en los sistemas electromecánicos. Es posible detectar ambos problemas eléctricos con analizadores de calidad eléctrica y cámaras termográficas.
- Las situaciones de desperdicio de energía se manifiestan como sobrecalentamiento y vibración excesiva, que son detectables mediante imágenes termográficas y medidores de vibración. Las causas probables varían, desde la refrigeración y el flujo de aire hasta el alineamiento de los rodamientos y otras causas de fricción. Escanee térmicamente los acoplamientos, ejes, bandas, rodamientos, ventiladores, componentes eléctricos, cajas de conexiones/terminaciones, devanados y de todo aquello que pudiese ser un indicador de operaciones ineficientes y desperdicio de energía.
- Como se mencionó anteriormente, una de las soluciones de ahorro energético más sencillas es registrar el consumo de energía en las grandes cargas electromecánicas a lo largo de un programa de operación completo. Determine cuándo la maquinaria emplea la mayor cantidad de energía (a menudo al arrancar) y compruebe si las horas de uso pueden ajustarse a las horas del día cuando las tarifas de la empresa pública son más bajas.
- Con ese mismo registro de corriente, compare el programa de operación con la frecuencia en que la máquina usa energía. ¿Cuánta potencia usa cuando no se está usando activamente? Sin el uso de controles, la mayoría de las máquinas debe apagarse manualmente, a fin de detener el consumo de energía, y las acciones manuales no siempre suceden. No es factible apagar toda la maquinaria, pero la mayoría puede ponerse en ralentí. Los controles varían entre los más simples y los completamente automatizados, pasando por el uso de sensores y temporizadores, hasta la maquinaria de ralentí flexible y las operaciones de codificado de forma rígida en un PLC.
- Clasificación de eficiencia y tamaños. Especialmente en las instalaciones más antiguas, los requisitos cambian pero las cargas permanecen iguales, lo que significa que en ocasiones un motor grande y costoso de arranque brusco permanece accionando un sistema con una intensidad de caballos de fuerza menor. La inclinación natural de todo gerente de una instalación es obtener el mayor tiempo de vida de una pieza grande de equipo. Sin embargo, vale la pena registrar cuánta potencia usa el motor, en comparación con los requisitos de carga actuales y con una unidad nueva, del tamaño correcto y alta eficiencia. Calcule cuánto exceso de energía se consume y multiplíquela por el programa de tarifas. Determine cuánto tomaría para que un motor nuevo se pagara a sí mismo; en ocasiones es conveniente remplazar un equipo antes de que falle desde el punto de vista financiero. De no ser así, considere si se pueden usar controles para modular la salida.
Vapor
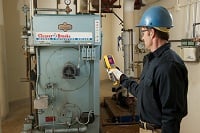
Es necesario inspeccionar las cuentas del proceso de calefacción de una parte considerable de los costos de operación y el sistema, a fin de evitar varios escenarios de distintos desperdicios de energía. Primero, registre el consumo energético en la caldera, para obtener un punto de referencia del consumo energético. Después, inspeccione el sistema de distribución, incluyendo las trampas de vapor, los manómetros, el aislamiento, las bombas y las válvulas. Use una cámara termográfica para detectar trampas de vapor con fallos, fugas, bloqueos, problemas de valores y fallas de condensación; el objetivo es devolver tanta condensación precalentada a la caldera como sea posible.
También puede usarse un detector de fugas ultrasónico para buscar fugas de vapor. Asegúrese de comprobar si hay aislamiento holgado o faltante y el correcto funcionamiento de todas las trampas de vapor; limpie el interior de las calderas y compruebe si hay bloqueos en las líneas de transmisión de vapor. La combinación de estos esfuerzos puede identificar desperdicios de energía y ayudar al equipo a planear soluciones de ahorro de energía, muchas de las cuales a menudo pueden implementarse mediante el mantenimiento en lugar de gasto de capital.
Aire comprimido
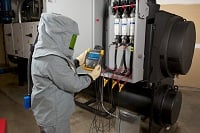
Un compresor de aire de 100 caballos de fuerza puede consumir electricidad con un valor de USD 50 000 anuales, y hasta 30 % de esa electricidad se destina a dar presión a aire que no se usa¹, a causa de fugas en la distribución y prácticas de desperdicio de uso. Y sin embargo, nunca se ha evaluado la eficiencia de la operación de aire comprimido de muchas instalaciones. De hecho, cuando se hace necesaria una mayor presión de aire, muchas instalaciones adquieren y operan un compresor adicional, sin darse cuenta de que pueden obtener más presión del sistema con el que ya cuentan.
Estudios del Reto del aire comprimido² han concluido que solo el 17 por ciento de los usuarios de aire comprimido consideran la eficiencia como un objetivo de la gestión del aire comprimido. Setenta y uno por ciento simplemente desean un suministro de aire constante y confiable. Esa filosofía es permeable hasta el punto del uso: las instalaciones de equipos neumáticos a menudo no cuentan ni siquiera con válvulas solenoides, operan el compresor de manera continua y el personal de base a menudo lo usa para limpiar el área de trabajo e incluso para refrescarse. En realidad, el aire comprimido es un producto bastante caro.
Para identificar y cuantificar el nivel de desperdicio, comience por registrar la corriente en un ciclo completo de operación en todos los compresores de aire. Ello establecerá cuánta energía se necesita para producir los niveles de presión de aire actuales. También registre las psi en la salida del compresor, en comparación con el punto de uso, determine el nivel de caída de presión y verifique el requisito de psi del fabricante para operar el equipo; no aplique presión excesiva "solo porque sí". Usar un módulo de presión conectado a un multímetro de registro es una manera de realizar estas pruebas sin invertir en equipo especializado. Finalmente, use un detector de fugas ultrasónico para escanear tanto de la línea de aire como sea posible, a fin de determinar la ubicación y el alcance de las fugas de aire.
Los pasos para mejorar la eficiencia energética incluyen reparar las fugas identificadas, configurar los compresores para generar solo la cantidad necesaria de presión, instalar válvulas solenoides de aire en el punto de uso y usar tanques de recepción para aplicaciones de gran volumen, en vez de aumentar la presión general del sistema.
¹”Improving Compressed Air System Performance: a Sourcebook for Industry” (“Mejora del desempeño del Sistema de aire comprimido: un libro de consulta para la industria”), sección 12, "Compressed Air System Economics and Selling Projects to Management" (“Proyectos de venta para la gestión y economía del sistema de aire comprimido”), pág. 69.
²Consulte el "Appendix D" de "Improving Compressed Air System Performance: a Sourcebook for Industry" en línea, en la dirección http://www.compressedairchallenge.org/library/#Sourcebook. Estudio encargado por el Departamento de Energía de EE. UU. (DOE) con soporte técnico del Compressed Air Challenge (CAC).