Maximizing VFD and UPS performance
If you are installing a variable frequency drive (VFD) or uninterruptible power supply ( UPS), or if you already have this equipment in place, you should be monitoring certain power quality parameters to maximize the performance of your equipment. To determine what power quality parameters to measure and when, start by understanding the power quality issues associated with this equipment as it draws current from incoming power in short pulses. VFDs and UPS systems are susceptible to power quality issues from the line power that supplies them, and they also produces harmonic currents that are reflected back into the distribution system.
The best practice is to monitor power quality before installation, to verify the supplied power to the equipment will meet manufacturer's specifications. Gather specific data for equipment manufacturers so they can analyze the harmonics and design filters to limit the amount of harmonic currents reflected back into the distribution system. Finally, monitor power quality during system operation to ensure the VFD or UPS does not exceed harmonic distortion limitations on the distribution system. Also use your monitoring data to ensure your power capacity is adequate, before installation.
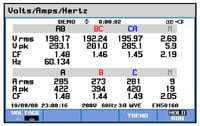
Prior to installing a VFD or UPS, measure power quality parameters on the feeder or branch circuit that will supply the VFD or UPS. Compare your data to manufacturers' specifications to ensure they are within spec. (Remember to save any recorded data to establish baseline data for future use!)
As an example, here are the input power requirements for one typical manufacturer:
- Voltage input +10% to -10%
- Frequency of 60 Hz (±5 Hz)
- Maximum Sag ride-through of 0% voltage for 1 cycle and up to 60% voltage sag for 10 cycles.
- Minimum 0.92 lagging power factor at full load with nominal input voltage
Swells, or too high an incoming voltage, can be one cause of an overvoltage fault. Sags or dips can cause an undervoltage fault on the equipment, shutting down the VFD or UPS.
To ensure the system will meet this manufacturer's specifications, use a power quality analyzer or recorder to monitor and record data. Recording data over a period of time will show what can be expected during an entire plant cycle. Then the data can be downloaded to a PC and analyzed. However, if you use a combined logger/analyzer, like the Fluke 435 Power Quality Analyzer, you can also take immediate checks on the incoming power while you're logging:
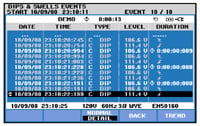
- Select "Volt/Amps/Hertz" from the main menu and observe Vrms and Hz are within the ±10% specification for voltage and within the ±5 Hz for frequency. (See figure 1)
- Select "Power and Energy" from the main menu and observe Displacement Power Factor (DPF) meets specifications. DPF is the power factor for the fundamental frequency while PF takes into account harmonics. DPF typically applies to manufacturer's specifications. (See figure 3)
- Though perhaps not required, it's a good idea to monitor incoming power for any harmonic distortions already created on the system from other sources. In many cases, a determination may have to be made to isolate the VFD or UPS on its own power source to minimize incoming disturbances. It is wise to have harmonic data to make such decisions before installation and, as always, save this data for future comparison.
- After logging is complete, select "Dips and Swells" from the main menu to verify Dips (Sags) do not exceed manufacturer's specifications. Use the "Events" table to determine the magnitude and duration of any dip. (See figure 2)
Be aware of situations unique to your equipment. For example, a static UPS system may have additional requirements on incoming power. While the acceptable voltage range may vary by manufacturer and allow voltage as low as 30% of nominal; some units may stop charging batteries at 15% below nominal voltage. Be sure to know your equipment's limitations by consulting the manufacturer's specifications.
Once the VFD or UPS is operating it presents another set of power quality issues that engineers and technicians must understand, know how to monitor and be prepared to correct: The effects of harmonics created by the VFD or UPS and the resulting Total Harmonic Distortion (THD) on the power distribution system. Engineers and technicians must understand how the voltage is distorted; determine the point at which to measure THD; and understand that limits are set based on distortion of the distribution voltage sine wave.
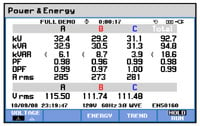
VFD's and static UPS systems operate by converting incoming AC power into DC. Then, by precisely switching this DC off and on, a variable voltage and variable frequency waveform can be produced. UPS systems switch the DC to provide "clean" power on the fundamental frequency to its critical loads. VFD's will vary frequency and voltage to adjust the speed of an AC motor. The conversion of the AC into DC in most VFD's and UPS systems is accomplished by a rectifier circuit. A capacitor is located across the output of the rectifier circuit. Power is drawn for the DC switching from this capacitor.
The capacitor draws current from the line (through the rectifier circuit), to charge itself during the peaks of the positive and negative half cycles. This draw of short current pulses results in a voltage drop. This produces a "flat-topping" of the incoming sine wave. Also, harmonic currents are created by the rectifier circuit. These harmonic currents flow back into the distribution system causing voltage and current distortion of sine waves in the distribution system.
What does all this really mean to the engineer and technician? Harmonic distortion must be monitored during VFD and UPS startup and corrected if limits are exceeded. And as mentioned earlier, if you provide the equipment manufacturer with the information, they can conduct harmonic studies and design filters to limit the harmonic distortion created by the VFD or UPS during operation.
Once any harmonic filters are installed and the systems are operating, monitor and record harmonic distortion created by the VFD or UPS. Since the IEEE Standard recommendations are based on the point of common coupling, setup and monitor at this point in the system. Typically, this PCC is the point where the VFD or UPS load feeder leaves a bus energized by a power source.
For example, to measure the effects of the harmonics generated by the VFD or UPS, set up the Fluke 435 at the PCC and then select "Harmonics" from the main menu. A Harmonic Graph displays the magnitude of each harmonic current in relation to the fundamental frequency of 60 Hz. Based on the type of drive or rectifier circuit in the VFD or UPS, technicians should expect higher magnitudes at certain harmonic frequencies. For example:
- A 6 pulse drive can be expected to generate greater harmonics at the 5th, 7th, 11th, 13th, etc., harmonic frequencies
- An 18 pulse drive can be expected to generate greater harmonics at the 17th, 19th, 35th, 37th, etc., harmonic frequencies
- A switch-mode power supply can be expected to generate greater harmonics at the 3rd, 5th, 7th, 9th, etc., harmonic frequencies.
In all cases, you should observe a decrease in the magnitude of harmonics as the harmonic order increases. However, be especially aware of any abnormal magnitudes at any harmonic frequency as observed on the harmonic graph. This could be an indication of the VFD or UPS harmonics creating a resonance situation with power factor correction capacitors in the system. Corrective action must be taken to avert this dangerous situation.
After viewing the harmonic graph for expected harmonic frequencies and making sure no abnormalities exist, select the "Meter" function to view the Total Harmonic Distortion for voltage. This should not be more than 5%. (See figure 4). Should this occur, determine the best solution to bring THD within acceptable limits. That could involve harmonic filters, isolation transformers or moving loads to other feeders or branch circuits.
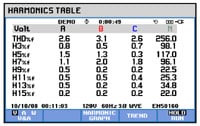
Keep in mind that monitoring, especially at the PCC, is an overall and longer term concept. Once you've established installation conditions, don't stop there. Return for periodic monitoring, and broaden your view to the entire power system. Evaluate your total maximum demand. It will change significantly over the long term, and as new devices and loads are introduced, they may impact what was once a clean supply to your VFD or UPS.
The bottom line when installing, operating and maintaining variable frequency drives and uninterruptible power supply systems is to provide good, clean, reliable power to this equipment as it operates and to minimize the harmonic distortions reflected back into the distribution system. Use power quality analyzers to monitor and record key power quality parameters prior to installation, during startup, and during normal operation. Technicians and engineers, working together with manufacturers, can use the observed power quality data to meet the ultimate goal: maximize VFD and UPS performance.