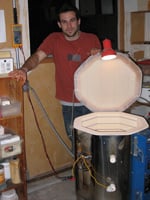
Adam Wegener makes and teaches ceramics in Portola Valley, CA. Last year, he bought a Fluke 189 DMM and a high temperature thermocouple from the local ceramics store that allows him to measure temperatures up to 2300 °F. Now he uses the 189 to log temperature over the 30-hour heat up and cool down cycle. Then, he loads the temperatures onto his computer and uses the peak temperature and heating rates to perfect his next firing.
As I learn more about ceramics, I become more aware of how much I don't know. This past summer opened my eyes to advanced ceramics making, including making glazes from scratch. I spent lots of time learning about firing my own kiln and how to perfect the process. The firing of a piece can make or break its final appearance. It is important to know what is going on in the kiln (by monitoring with my thermocouple and DMM) because different chemicals in the glazes melt at different temperatures. It is important to fire to the temperature your clay and glazes are made for to achieve maximum strength and food-safeness. As the kiln heats up, it does heat work on the pieces, so it is not only important to monitor the temperature but also the rate of heat up and cool down.
Ceramics utilize a temperature scale of different "Cones" of composite materials that are manufactured to bend when a specific amount of heat work has been done. Orton is the company that supplies these Cones. Temperatures for ceramics range from low fire (1200 °F) up to high fire (2400 °F). When talking about temperatures for firing ceramics, one would refer to the temperature by saying "Cone 5" (which would correspond to 2200 °F peak temperature). The Cone numbers and their corresponding temperatures of maturity are listed on Orton's web site. Temperatures go like this (a preceding 0 acts like a (-) sign, and the scale is like an absolute number line:
Cone 022 (1094 °F), Cone 021…Cone 05 (1911 °F), Cone 04…Cone 1, Cone 2…Cone 5 (2205 °F), Cone 6…Cone 10…Cone 12 (2419 °F).
When I fire my ceramics, the initial firing is called a Bisque firing. This initial firing is to Cone 05 (1911*F) and gives the pieces some strength and makes them porous so they will absorb the glaze. The pieces are then dipped in glaze and fired again. This second firing is called the glaze firing. Different glazes are made for different "cones". I glaze fire to Cone 5 (2205*F), and this means that the clay and glazes I use will be optimal for strength and food-safeness at this temperature. Monitoring the firings with the DMM helps me identify why I may be getting imperfections in my results. Many times rapid cooling can cause glazes to bubble and not result smooth.
Usually you stay with what you get when you take things out of the kiln. If you don't like the glaze on a piece, it is very difficult to try to apply glaze again and refire because the piece is no longer porous. With refiring, you run the risk of your pieces cracking or getting more messed up. I have refired sometimes to eliminate glaze bubbles. This refiring allows more heat work to be done on the piece, and the glaze will become liquid-y again and smooth over. Different temperatures of firing can change the color results of the glazes. Firing too hot can cause the glazes to run off the pieces onto the kiln shelves, a big mess to clean up.
Mostly I perfect my firings by making adjustments based on the previous firing. Each firing I try to get a little better than the last. Things to shoot for in a perfect firing are consistency throughout the kiln, proper heating and cooling rates, and peak temperature reached but not exceeded.
I use my multimeter by placing my thermocouple in a "peep hole", a hole in the side of the kiln that allows for looking into the kiln during firing. I set my logging interval for 5 minutes and the DMM records the temperature. The entire process usually lasts 24 hours for heat up and cool down. Heat up usually takes between 8 and 10 hours. After each firing, I load the data on to my computer and print out the graph. I check the heating and cooling rates throughout the firing to see if they were what I was going for. I can compare firings from different dates to see if and heating elements may need to be replaced.
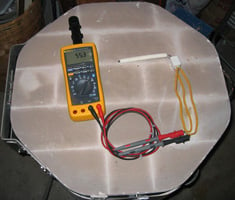
The DMM has helped me identify kiln problems. When using the kiln at school, we kept getting an error from the kiln. We never knew what was going on until I used my multimeter to diagnose the problem. By logging the temperature, we realized that the kiln was not getting up to the peak temperature, most likely because it was not getting enough power. It was nice because we didn't have to stand around and wait for it to mess up for 10 hours. I just left the meter, came back the next day and loaded the data on my computer.
I use kilns that are older models, and many improvements in firing control have been made since my kilns were made. Newer kilns use on-board computers and thermocouples to adjust the temperature as the kiln fires. Users can program in the firing cycle to the kiln computer and the kiln does the rest. My kiln is manual, so I adjust the speeds and temperature shut off by hand. Either way, it is nice to have a separate thermocouple system to record what's happening in the kiln.